5G technology triggers age of smart factories and digital transformation of manufacturing
- Leading global ICT provider Huawei Technologies and electrical appliance maker Midea team up to open Southeast Asia’s first fully 5G-connected factory
- Thai facility – one of the region’s largest air-conditioner makers – uses AI, smart data and cloud computing to boost efficiency and cut production errors
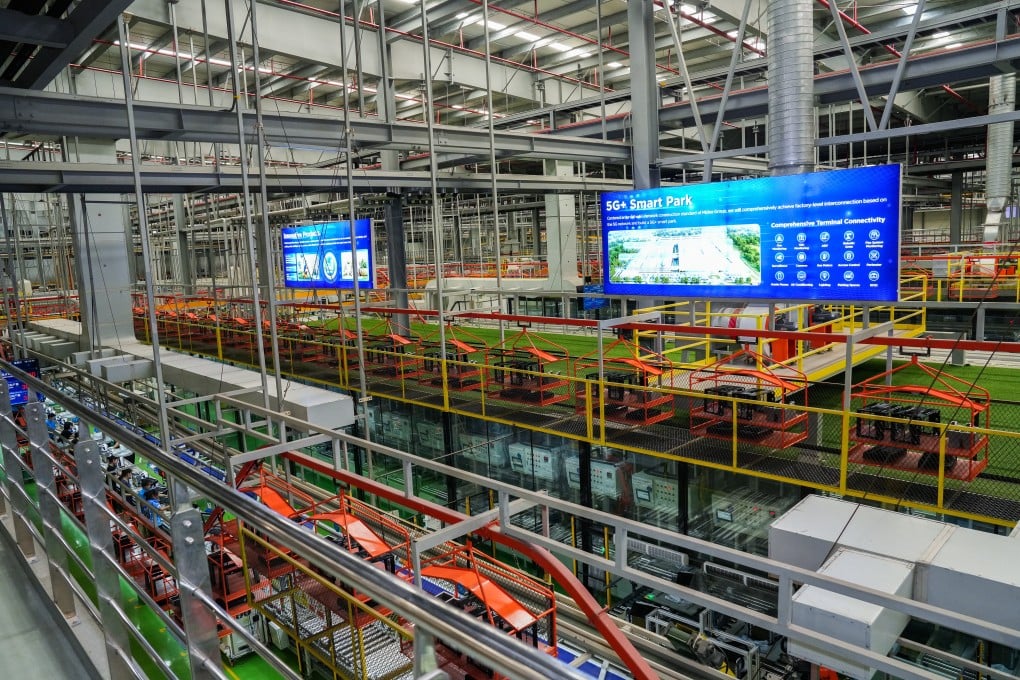
In recent years, digital technology has broadened the scope for innovation in the manufacturing industry. The use of artificial intelligence (AI) and 5G (fifth-generation mobile communications technology) networks offer a variety of benefits including better production efficiency, reduced operational errors and higher product quality. Employing these technologies in factories is quickly becoming essential for companies if they wish to stay competitive in a digital-first future.
Research by Fortune Business Insights suggests that the value of the smart manufacturing industry is expected to grow from US$310 billion in 2023 to US$745.1 billion by 2030. As it stands, Asia-Pacific holds the largest market share in this industry, and it is also predicted to be the fastest-growing region during the next decade.
Last month, Southeast Asia’s first-ever fully 5G-connected factory was opened in eastern Thailand, following a collaboration between Chinese electrical appliance manufacturer Midea, Huawei Technologies, the global provider of information and communications technology infrastructure and smart devices, Thai mobile phone operator Advanced Info Service (AIS) and telecommunications operator China Unicom.
The facility at Chonburi Industrial Park, in Chonburi province, makes air conditioners using technologies, including 5G, AI, big data and cloud computing. It is Midea’s first such factory outside China, and is now one of the region’s largest air-conditioner production bases.
“In line with Midea Group’s strategy of full digitalisation and full intelligence, the Thailand 5G smart factory sets the blueprint for the future of manufacturing, where each production phase is seamlessly connected, and the overall operating efficiency has been improved by 15 per cent to 20 per cent,” Vincent Cai, general manager of Midea Thailand Air Conditioning Factory, said.
Midea’s factory is a prime example of how industrial processes can be modernised using full 5G connectivity across the factory floor. Production devices can be monitored and analysed in real time, with the collected data helping to ensure that all the equipment is being used optimally.