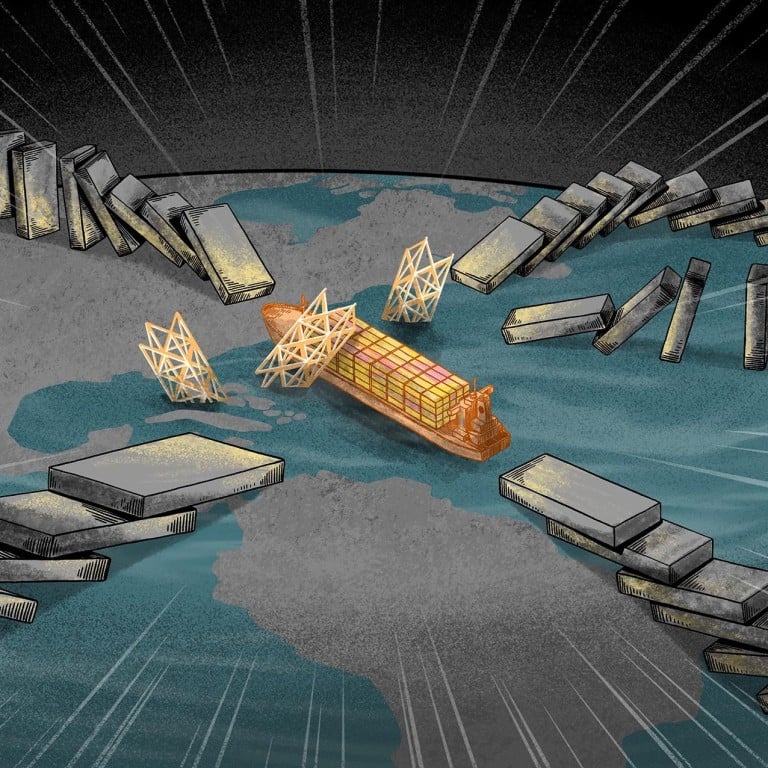
Baltimore bridge disaster tests supply chains’ resilience but pandemic lessons ease impact
- Since the pandemic, US East Coast ports have invested in expanded container terminals, adopted new technology for inventory management and made other upgrades
- Ripple effects from the Baltimore port’s closure are expected to extend to Europe, Japan, India, South Korea and Mexico, which have close trade ties to the US
With no work emails or phone calls it’s mostly been “scary quiet” for Theresa Abel since March 26, when a huge container vessel crashed into Baltimore’s Francis Scott Key Bridge, bringing down the span, killing six workers and clogging the main shipping channel that connected the city’s port with the rest of the world.
Abel, a manager at a logistical support and transport services company, described the sudden disruption at the harbour, the ninth largest for international shipments by volume in the US, as “worse than the Covid-19 pandemic”.
From 2020 through 2022, Covid-induced stay-at-home orders, a disproportionate spread of the deadly virus and an unexpected boost in consumer demand for goods led to a global supply chains crisis, high shipping costs and inflation that still persists.
By comparison, Abel said that “during the pandemic the port was still running but on major restrictions. This incident has caused a standstill.”
Last week, salvage crews managed to remove a massive piece of steel from the bridge wreckage but thousands of tons of twisted metal and concrete debris still remain on the ship’s deck since the crash.
As of April 19, some 120 containers had been taken off the vessel, which continues to block access to the port. It was carrying 4,700 containers at the time of the crash, but engineers aim to offload about 178 to refloat it.
Two temporary channels have been opened to ensure some access. But they are not deep enough for cargo vessels, which have been diverted to other US ports since the bridge collapse.
On Monday, a third passage with a controlling depth of 20 feet was opened to what the Baltimore port officials described as “commercially essential vessels” until the main channel is reopened. A full restoration of maritime traffic is being aimed for the end of May, according to Maryland Governor Wes Moore.
‘We must address this issue’: Panama Canal traffic cut by 36% due to drought
But before that happens, analysts predict reverberations will be felt by US supply chains and shipping lines, which are already re-routing to avoid the Red Sea because of attacks from Houthi militias of Yemen, the war in Ukraine and delays at the drought-hit Panama Canal.
Although the Port of Baltimore handled only 4 per cent of the total trade volume among US East Coast ports, redistribution of trade due to the Key Bridge collapse and maritime disruptions could also affect operational capacity and logistics across the broader East Coast port network.
According to a report from credit rating agency Morningstar DBRS, the collapse could become the most expensive marine insured loss in history, estimating a total insured losses of US$2 billion to US$4 billion. The White House says its goal is to rebuild the bridge in about two and half years.
Since the pandemic, East Coast ports have gained new significance as Biden’s strategy of “friendshoring” has increased trade with Europe and Asian countries like Vietnam, Bangladesh, Indonesia and India.
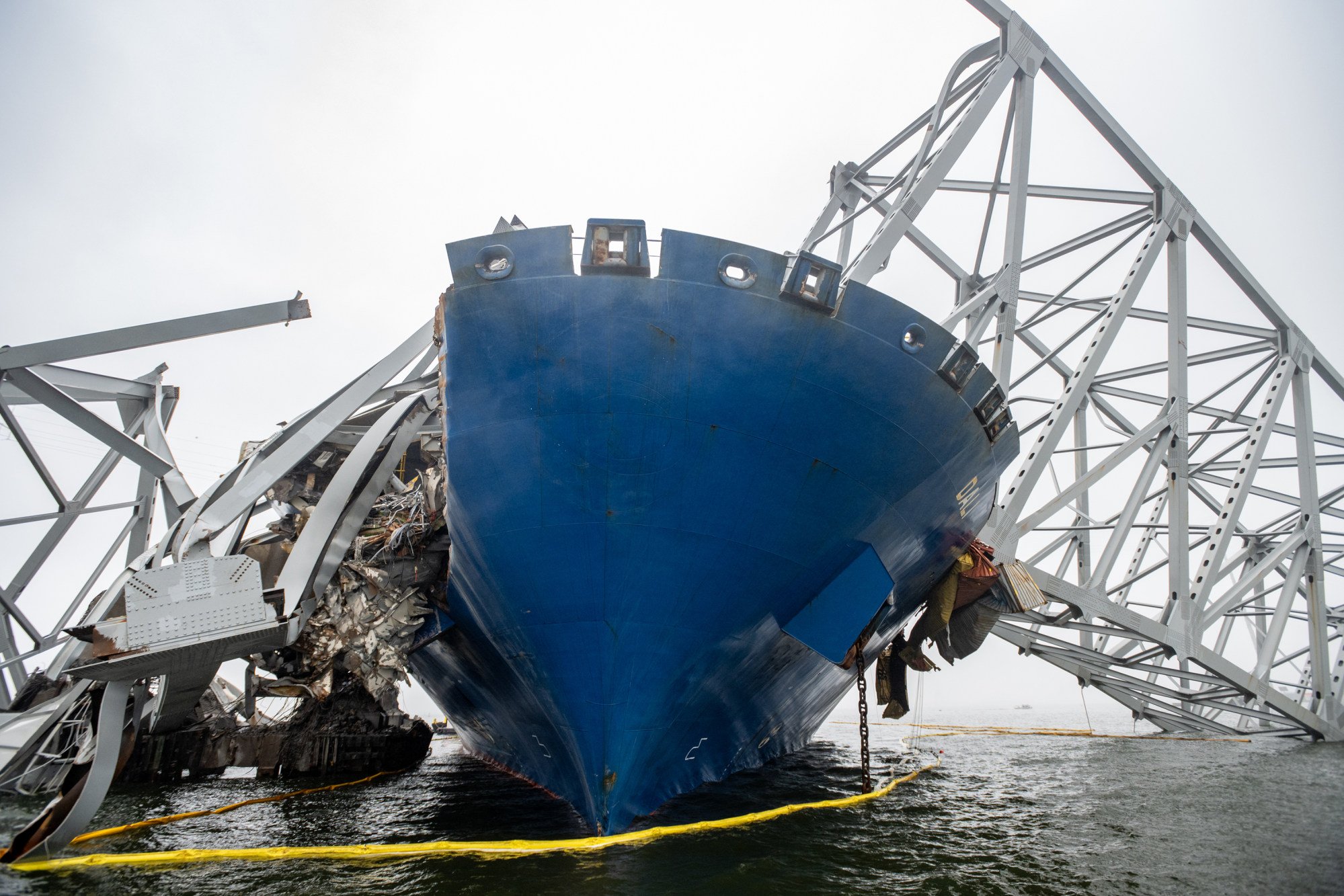
With that growth, these ports have invested in expanded container terminals, adoption of new technology for inventory management, upgraded road and rail connections, and enhanced facilities to handle perishable goods.
Now supply chain experts expect the Baltimore bridge collapse to catalyse long-term shifts in the landscape of US port operations and supply chain strategies.
According to Zongyuan Zoe Liu of the Council on Foreign Relations, a think tank in New York, the response to the temporary closure of the Port of Baltimore “demonstrates the resilience of US supply chains despite fears of costly disruptions”.
She said that although the disaster has caused a “logistics challenge”, there has not yet been a major supply chain crisis, adding that the re-routing to other US ports is likely to “exacerbate congestion” in ports and highways along the East Coast and “raise labour costs” because of additional demand for services, trucks and truck drivers to move goods.
“Meanwhile, the bridge collapse is diverting an estimated 5,000 trucks per day, carrying US$28 billion in goods, leading to delays and raising fuel costs for shippers and their clients,” she said.
Baltimore bridge could take months to reopen, hitting sectors from cars to coal
Nick Vyas of the University of Southern California’s Marshall School of Business said the ripple effects would extend to places like Europe, Japan, India, South Korea and Mexico, which are closely tied to the US through trade in automobiles and energy.
He said the disruptions highlighted the “interconnected nature of international trade”, adding that the full scope of the disruption and its long-term effects on international trade are yet to be fully understood.
Last year, the Port of Baltimore handled 52.3 million tons of foreign cargo worth nearly US$81 billion. It was the second busiest for coal exports, accounting for 28 per cent of total US coal exports in 2023.
The top consumers of US coal included India, China, Japan, the Netherlands and South Korea. Measured by tonnage, China was the port’s No 2 import and No 3 export trading partner in 2023.
But China does not count the US among its major coal suppliers; most of its imports come from Mongolia, Australia and Indonesia.
The US Energy Department said on April 9 that coal exports would be down by 33 per cent for the month, and by 20 per cent in May, because of the situation in Baltimore.
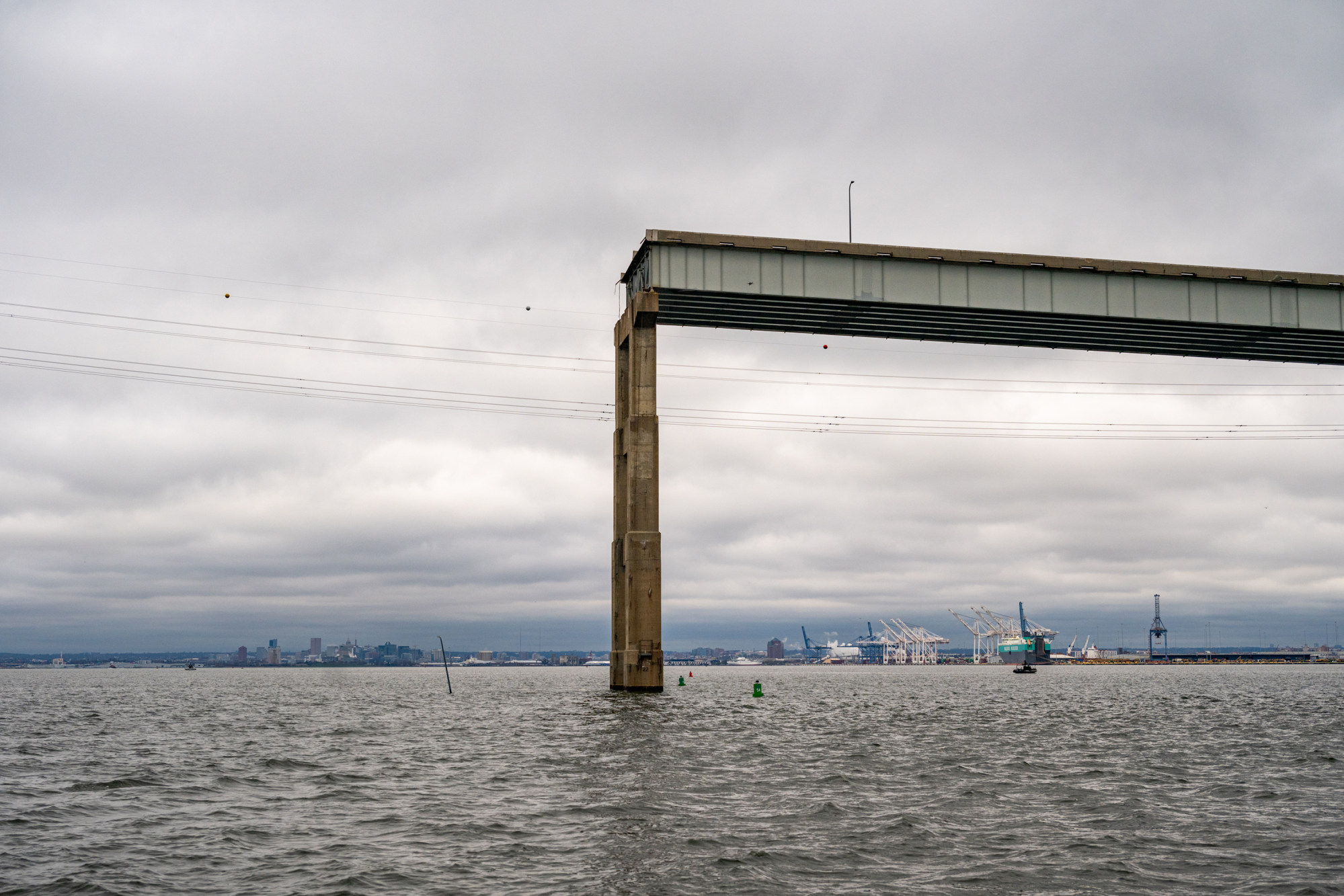
The agency expects US exports to fall by 6 per cent for the full year, a reversal from its previous forecast of 1 per cent growth. US coal exports account for about 6 per cent of the global supply.
“We expect US coal exports to recover toward the end of the summer or early fall, but there is significant uncertainty based on the timeline for the port reopening,” said Joe DeCarolis, who leads the US Energy Information Administration.
The port also moved about 1.3 million tons of farm and construction machinery and 750,000 cars and light trucks last year, more than any other US port.
“Baltimore is like the Taylor Swift of American auto ports,” said Tinglong Dai of Johns Hopkins University’s Carey Business School in Washington.
“If she didn’t perform as scheduled, the world would immediately feel a great sense of loss,” he said, adding that the supply chain resilience built since the pandemic years should help limit disruptions unless recovery efforts are “relentlessly” slow.
Huge crane ready to clear Baltimore bridge debris
But for Vyas, how much other ports in the US can handle extra goods is a major question, even though American ports have upgraded their gear and tech to move things faster and handle bigger ships in recent years.
“For example, ports like those in New York and New Jersey are well placed to take on more because they’ve been beefing up their capacity,” he said. “But there’s a catch.”
According to Vyas, even though many ports are ready for more work, they can take on only a limited amount of cargo.
“If a port is already super busy, squeezing in more shipments could cause delays and cost more. Plus, not all ports can handle every type of cargo – some are better with cars, others with containers or bulk goods,” he said.
So far, other US ports have been able to absorb the cargo previously handled in Baltimore, but things could get tough in the long run.
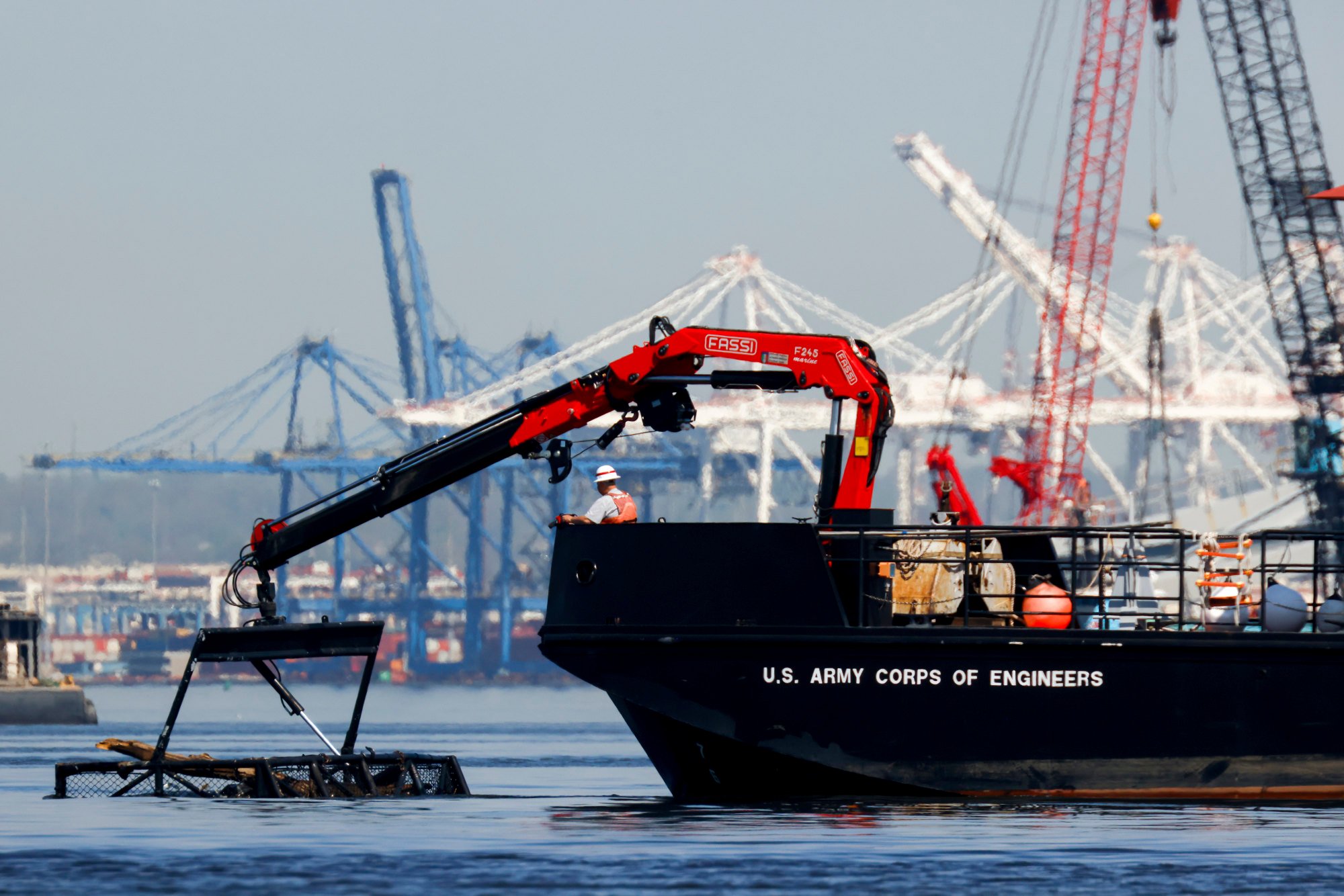
Griff Lynch, chief executive of the Georgia Ports Authority, said that some areas in that state were getting crowded and that there was “no way” all of Baltimore’s vehicles could be moved by Georgia’s facilities. This month, the state’s ports are expected to handle 20 per cent more vehicles than usual.
Beth Rooney, a director at the Port Authority of New York and New Jersey, said her facility had the capacity to handle “all Baltimore cargo temporarily diverted here”.
The New York and New Jersey ports handled about 25 to 28 per cent more cargo than usual during the pandemic, but Rooney said that despite having “more than enough capacity”, cargo remained “fluid”.
“So if for some reason that cargo does not leave our terminals in a timely manner, then we could expect to see efficiency issues. And that’s obviously not something that anybody wants to see,” she said.
According to Gene Seroka, executive director of the Port of Los Angeles, his port has yet to see cargo diverted from Baltimore. Cargo owners had already begun shifting their goods to the West Coast and the LA port because of geopolitical tensions in the Red Sea and low water levels in the Panama Canal, he said.
How Beijing’s Marco Polo Bridge shaped modern Chinese history
“The unfortunate incident in Baltimore may eventually impact West Coast cargo as well,” he said, adding that the port was currently operating at about 75 per cent capacity and had the potential to meet future demands.
Vyas said he anticipated new trends like a surge in investment towards enhancing infrastructure of ports nationwide and a strategic diversification of the supply chain and broader utilisation of ports for a more balanced distribution of cargo traffic.
But, he added, another unforeseen event could upend the current calculations and planning.
“[It] could be anything: a global pandemic that turns our supply chains into spaghetti, geopolitical tensions that add an extra layer of complexity, or a bridge collapse in Baltimore that throws a wrench into the logistics of getting our favourite goods from A to B,” he said.
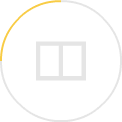