Why recycling isn’t working in Hong Kong: battery recovery plant is idle most of the time – is apathy or smuggling to blame?
- The brainchild of actress Sharon Kwok, her tycoon husband and friends, battery recycling centre is grossly underused, like its Hong Kong Eco-Park neighbours
- Lead-acid batteries used in vehicles can be 95 per cent recycled, but the plant doesn’t receive enough of them. It may be another victim of recycling apathy
Hong Kong’s Battery Recycling Centre has been ominously quiet for some time. On a recent visit the mainly bright blue machinery and yellow safety fencing were still spick and span.
It’s not supposed to be like this. Instead, the box-shaped, three-storey structure in Hong Kong’s EcoPark should be busy and noisy, smashing used lead-acid batteries to bits, cleaning and purifying their components and producing recycled products, especially lead.
The plant’s interior is reminiscent of the first Terminator movie – with conveyor belts, steel gantries and stairways, machinery including outsize generators, and piping connecting enclosed tanks and vats.
The Battery Recycling Centre is the brainchild of Stanley Pong Kit, who is ranked by Gafencu luxury magazine as one of “the 300 Most Powerful People in Hong Kong”. In person, Pong is down-to-earth and fond of recalling his student days in a band whose lead singer went on to form the Eurovision Song Contest-winning British pop group Brotherhood of Man.
The plant was first set up partly because Pong had extensive metallurgy experience working with Shiu Wing Steel, which was established by his father, Pong Ding-yuen, and partly because he is married to actress-turned-conservationist Sharon Kwok Sau-wan. While profits from the recycling plant would be a bonus, it is chiefly a social venture, aimed at solving a serious issue that few environmentalists are even aware of.
“When most people think of batteries and recycling, they think of the small AAs and AAAs,” says Pong. “But about 95 per cent of batteries by weight are lead-acid batteries. They’re mainly used in transport – providing sparks for ignition in internal combustion engines, even as backup batteries in electric vehicles.”
Data centres can use lead-acid batteries, he adds, and certain critically important street lamps are powered by them.
“While lead-acid batteries aren’t as efficient in terms of storage as lithium batteries, they’re cheap, stable and reliable,” Pong says.
The lead-acid battery was invented by French physicist Gaston Plante in 1859. They store electrical energy that is released when sulphuric acid interacts with lead oxide and lead to form lead sulphate and water. While they can be recharged, over time their efficiency declines and they must be replaced – perhaps every two or three years. This regular replacement can lead to problems if the batteries are not properly recycled.
In Hong Kong’s rural New Territories, these problems have included the dumping of battery sulphuric acid on farmland.
Yet lead-acid batteries can be recycled without environmental damage – with recycling rates of 90 per cent or more in countries such as the United States. There was simply no facility for that kind of activity in Hong Kong until Pong stepped into the breach.
Though he now speaks passionately about his project, Pong is hardly a typical greenie. His father was a successful real estate developer in the 1950s, he says.
“He had five sons and wanted us to work for a living. My elder brothers studied engineering, and Hong Kong then had a problem buying high-quality steel, which was imported from countries including Belgium and Japan. Some local mills rolled steel from ship plates to form thinner steel sheets of a manageable size, and my dad thought, ‘This must be a good business for my family’,” he explains.
This park deserves a lot more. We’ve been here all afternoon, but did you see a truck come in? No
Pong’s father established Shiu Wing Steel in 1956 and, with two of Stanley Pong’s brothers, bought scrap from Europe to make a rolling mill in Tseung Kwan O. Pong joined the business in 1973, after obtaining a degree in metallurgy from Leeds University in Britain, and an economics degree in Japan.
He learned about the problems with lead-acid batteries from a friend in Hong Kong’s Environmental Protection Department, who also noted the batteries can be 95 per cent recycled back to their raw materials.
Pong discussed the issue with a friend, who was concerned about possible battery acid poisoning on Tuen Mun farmland, and with other friends they collaborated to establish the Battery Recycling Centre. This was eight years ago. Like the course of true love, establishing a recycling centre in Hong Kong does not run smooth.
Frustrations included ensuring the facility would meet government specifications, which were mostly adapted from international regulations. Then Pong had to find the best way of recycling the batteries.
With his wife and partners, he journeyed to North America, western Europe, Romania, India, mainland China and Taiwan to look at recycling technologies and find the best equipment they could.
Pong was surprised that one of the best suppliers was a team of young Chinese engineers with fresh ideas such as blasting fragments of plastic battery casings with water jets, rather than sorting the fragments using gravity as traditional plants do.
“Wow, I’m impressed,” thought Pong – who is clearly proud of the powerful water jets, which ensure faster and more thorough separation of the plastics and require fewer chemicals for acid neutralisation. “You don’t want to put your hand in,” he says.
By August 2019, the machinery, piping, vats and more had been connected and tested, and the Hong Kong Battery Recycling Centre became operational.
After a couple of men with a forklift have shifted the batteries – which are roughly the size of bulky toolboxes – the recycling process becomes fully automatic. A conveyor belt takes the batteries to a machine where they’re crunched to bits, with the plastic fragments then sprayed clean and tumbled down a chute to a barrel. The heavier lead particles are separated and cleaned, while the liquid is chemically treated to remove acid and extract more lead.
Pong aims for an additional phase, to remove other heavy metals, which could contaminate the water the facility reuses. But right now, the main products are plastic pellets, calcium sulphate and sodium chloride – or salt and lead. And it’s only the lead that has sufficient market value to ensure the facility at least pays for itself.
Although it can handle 10 tonnes of batteries an hour, the recycling centre is too often idle, and economic viability seems a distant goal. Yet Hong Kong should have enough lead acid batteries for recycling. Using studies from the United Nations and other organisations, Pong estimates the city disposes of at least 22,000 tonnes of lead-acid batteries each year.
If we get 50 per cent of the batteries available here, we may be all right. If not, we could become another victim of the Hong Kong EcoPark
It seems many of these batteries “vanish”, even though none are now permitted in landfills.
Pong believes those mysteriously missing batteries may be smuggled out of Hong Kong, after the acid is tipped out, so unlicensed smelters can produce lead. While there are companies supporting the centre by supplying batteries – including the Stock Exchange of Hong Kong, Towngas, Hong Kong Broadband and the Swire Group – he believes many more organisations would follow suit if the government enforced existing regulations on the disposal of lead-acid batteries.
“If we get 50 per cent of the batteries available here, we may be all right,” says Pong. “If not, we could become another victim of the Hong Kong EcoPark.”
His gloomy prognosis is partly based on information from neighbouring recycling organisations, which are all frustrated at receiving barely a trickle of the materials – including used cooking oil, rubber tyres, waste wood and more – that they need to survive.
“This park deserves a lot more,” Pong says. “We’ve been here all afternoon, but did you see a truck come in? No.”
At last, one of the plant’s two trucks, painted yellow as a daffodil, does arrive, and two men unload batteries, adding them to a small stack in the corner of the centre, which is otherwise silent. It’s a sad testimony on the state of Hong Kong’s recycling industry.
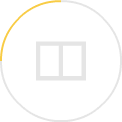